产品描述
矿制酸成套技术是指以硫铁矿制酸的沸腾焙烧、烟气净化、制酸、尾气脱硫、废酸废水等各环节为基础,覆盖硫铁矿制酸,金精矿制酸,锌精矿制酸,锰矿制酸等多种矿制酸系统的技术。单套系统配套达12~40万吨/年制酸不同规模。
硫铁矿制酸一般由原料、焙烧、净化、转化、干吸、尾吸、成品等工序组成。
典型的400kt/a硫铁矿制酸工艺流程见下图。
典型的400kt/a硫铁矿制酸工艺流程
原料工序:从选厂运来的合格的硫精砂先进入原料库房,再由桥式抓斗机送入贮斗,经两级蒸汽干燥工艺后,水分降至8%左右,通过胶带输送机输送至加料房的加料料斗。
焙烧工序:硫精矿原料从加料料斗通过加料皮带、计量皮带、转料皮带及星型给料机分别送入沸腾炉的二个加料口内,在沸腾炉内与来自空气鼓风机的空气混合沸腾焙烧。焙烧所产生的含S02~13.5%、温度~950℃的高温烟气,经废热锅炉回收部分热能,温度降至~350℃后,依次通过旋风除尘器和电除尘器,使炉气中尘含量降至≤0.1g/Nm3进入净化工段。
来自废热锅炉的高温矿渣经过风冷埋刮板输送机,会同来自沸腾炉的高温矿渣分别进入浸没式冷却滚筒;来自旋风除尘器及电除尘器的渣尘分别通过回转阀与来自浸没式冷却滚筒的矿渣一并进入下一个浸没式冷却增湿滚筒进行继续降温,温度降至70℃。冷却后的矿渣经带式输送机转运至渣场后运出。
净化工序:来自焙烧工段的炉气进入动力波洗涤器,净化工段动力波洗涤器采用10%稀硫酸对焙烧烟气进行绝热增湿洗涤,被洗涤后的炉气温度由280-320℃降温至~67℃,炉气中大部分矿尘被洗涤进入稀酸中。炉气再进入填料塔洗涤,用3%稀硫酸进一步洗涤除去炉气中尘、As、F等杂质,炉气温度降低至40℃以下,进入电除雾器除雾,炉气经净化后去干燥塔。
干吸工序:经净化后的炉气进入干燥塔,用93%硫酸喷淋吸收净化气中的水份,使净化气中的水份降至
转化工序:转化工段工艺流程采用3+1两次转化,即Ⅲ、Ⅰ— ⅣⅡ 换热流程。来自S02风机的净化气,依次经过Ⅲ、Ⅰ换热器管间,与转化器三段、一段出来的高温S03气换热,温度升至410℃左右进入转化器,经一、二、三段转化,换热后的转化气进入第一吸收塔,吸收其中的S03。第一吸收塔出来的气体再依次经过Ⅳ、Ⅱ换热器的管间与转化器四段及二段出来的高温转化气换热,温度升至425℃后进入转化器四段,经转化器四段进行转化后,气体分别经Ⅱ、Ⅳ换热器换热,温度降至~165℃进入第二吸收塔,转化系统总转化率可达99.8%。
冶炼烟气制酸工艺没有上述硫铁矿制酸的原料和焙烧工序,其他后续工序与硫铁矿制酸类似,有净化、转化、干吸、尾吸、成品等工序组成。根据不同的金属冶炼品种和冶炼工艺,冶炼烟气制酸也有其独特的特点。
(1)是气量和气浓波动比较大。制酸工艺要求气量稳定和气浓适中。但是,冶炼烟气则很难满足这些要求。特别是目前普遍采用的转炉烟气,不仅出现周期性的气量和气浓变化,而且还因频繁地进行加料、排渣和出料而导致停止送风的间断现象。这给制酸系统带来一定的困难。
(2)是二氧化硫浓度有的比较低。除了锌精矿或铜精矿采用沸腾炉氧化焙烧和铜精矿闪速熔炼烟气气浓可达10%-13%,锌业矿沸腾炉硫酸化焙烧气浓可达8%~9%,其余冶炼烟气的气浓均较低,转炉烟气在二周期理论上可达21%,但是由于加料、排渣所造成的间断和烟罩的大量漏风,也不能将它们列为高浓度的烟气之列。铅锌烧结机烟气浓度为4%~6.5%;密闭鼓风炉(铜)烟气3%~5%。其次,鼓风炉、电炉、反射炉等烟气浓度更低。
(3)是冶炼烟气的成分较复杂 在冶炼烟气中,不仅含有二氧化硫和三氧化硫,而且还有较硫铁矿制酸烟气更多的粒度更细的金属氧化物粉尘。这些粉尘有的是以蒸气状态挥发出来,当温度降低后,就冷凝成为极细颗粒。例如,铅、锌、锑、铋、镉、硒、碲、铊、砷等杂质。要除这些杂质需要采取较复杂的净化方法。除此之外,还有氟化氢、一氧化碳、二氧化碳等气态杂质以及大量的水蒸气,这都给制酸带来一定的困难。因此,对炉气净化工序要求较高。
关键词:
2、矿制酸技术
免费获取产品报价
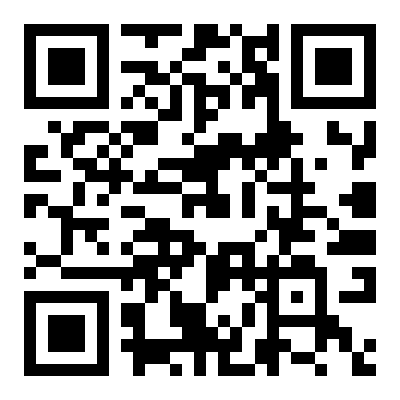
扫描二维码